Quality Control and Laboratories
The Quality Control and Laboratories unit comprises the following sections:
• Steelmaking Laboratory
• Quality Control of Production
• Central Laboratory
• Rolling Laboratory
Steelmaking Laboratory
The steelmaking laboratory analyzes products from the melting and casting sections using Spectro quantometers, ON, ONH, and XRF devices according to the grades produced. Samples are typically taken from the EAF, LF, tundish, and final product (produced billets) under normal conditions and delivered to the laboratory for elemental analysis.
Chemical analysis of slag is highly important. Analyzing slag is directly related to the consumption of refractory materials and furnace energy, as well as the removal of harmful elements and its use as acoustic and thermal insulation. Therefore, slag samples from the LF and EAF sections are chemically analyzed using XRF devices.
For high-quality grade steels, the concentration of gases in the product must be controlled to produce high-quality products that meet customer specifications. To measure the amounts of nitrogen, oxygen, and hydrogen, samples from the EAF, LF, and final product (produced billets) are analyzed using Eltra ON900 and Leco ONH836 devices.
Quality control of manufactured products
Produced ingots with different grades and sections are coded by the quality control personnel of the product warehouse and checked for appearance defects in hot and cold inspections and finally classified. All these operations must be approved by ingot quality control experts.
These defects include external defects and internal defects as follows:
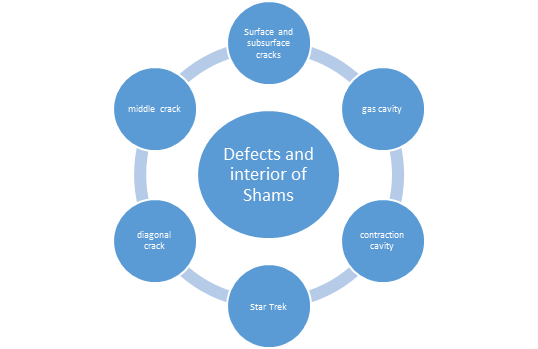
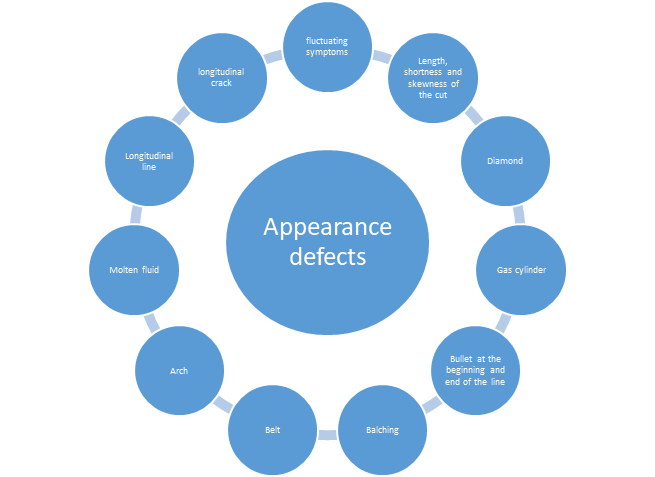
Monitoring the performance of warehouse personnel (inspectors) includes overseeing the inspection process, coding, accuracy of classification, arrangement, labeling, compliance with customer orders and desired standards, loading, and more. This supervision is conducted by quality control inspectors (experts) for billets - rolling and NDT (Non-Destructive Testing) experts. Random checks of classifications and follow-ups for sampling of laboratory specimens are conducted as needed.
Central laboratory
The central laboratory consists of several separate laboratories:
• Quality control of incoming and production raw materials
• Physics lab
• Chemistry
• XRF laboratory
• Water laboratory
• Gas Laboratory (GC)
• Oil laboratory
Quality control of raw materials
The quality control of all incoming raw materials, production materials, slag, water, gas and oil is done in the central laboratory.
From raw materials entering the factory that are used in the production line, such as iron ore concentrate, pellets, types of ferroalloys, types of coke and CPC, calcium aluminate, types of lime and dolomite, bentonite, etc. by sampling personnel. Sampling is done and they are transferred to the central laboratory for physical and chemical analysis.
Physics lab
The works and tests that are performed in the physics laboratory include the preparation of samples for chemical analysis and various physical tests. In the process of sample preparation, preliminary crushing, powdering, sieving and coding of the sample are done.
The procedures performed in the physics laboratory include:
• Abrasion strength of ball (tumbler)
• Size distribution (granulation test)
• Preparation of samples
• Bulk density measurement
• Compressive strength of CCS fired pellets
• Compressive strength of DCS dry raw pellets
• Compressive strength of raw GCS pellets
Chemistry lab
The samples prepared in the physics laboratory are sent to the chemistry laboratory for chemical analysis and the desired tests are performed on the sample.
For example, total iron, metallic iron and carbon/sulfur samples are measured for sponge iron samples, total iron, iron oxide (FeO) and carbon/sulfur are measured for pellets and concentrates.
XRF lab
Elemental analysis of powdered solid samples is performed using an X-ray fluorescence diffraction (XRF) device. The preparation of samples for analysis is performed by two pressing methods (using a press machine) and fusion method (using a furnace and melting the sample).
Water laboratory
Considering that the monitoring of industrial water used in different production units of the factory in order to control the amount of corrosion and sediment is of great importance, therefore, for this purpose, on a daily basis and according to a predetermined schedule, about 40 samples from regeneration units, pellets Forging, rolling and steelmaking and parts of the treatment plant, WTP are sampled and sent to the water laboratory for the desired analysis.
Gas laboratory
The analysis of reduction gases (reduction unit) is performed in the gas laboratory (GC). According to the predetermined program, samples are taken from Process, Reform, Bustle, Cooling, and Natural Gas sections and analysis is done by Gas Chromatograph. Considering that the percentage of compounds of each of the samples should be in the desired range, therefore their analysis is of great importance.
Oil laboratory
The analysis of used and new oils used in the equipment of different parts of the factory is done in the oil laboratory. In order to prevent the depreciation of devices and equipment and to idealize their life span periodically (weekly, monthly and annually) and based on a predetermined schedule, the oil of the equipment located in different units is sampled and analyzed Quality and control are transferred to the oil laboratory and the desired analysis is performed based on the type of oil and equipment.
Rolling laboratory
The quality control of final products, including production ingots and rolled ingots, is done in the rolling laboratory. In general, the physical properties, mechanical properties and internal defects of the ingot are investigated. In order to check physical properties, analyzes including cleanliness test, grain size, microstructure, and decarbonization are performed and evaluated, and tensile, impact, firmness, and hardness tests are also performed to check mechanical properties. To check the internal defects of casting and rolling products, macrowatch and sulfur print tests are performed.